The Federal Factory of the Future: How AI is Transforming Manufacturing
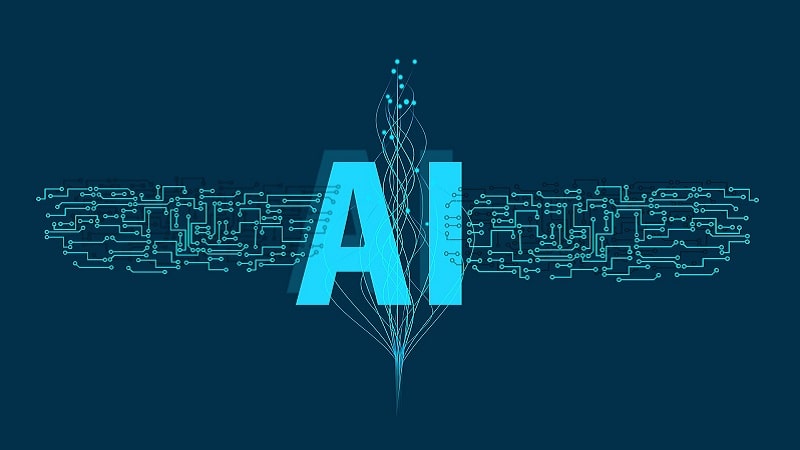
By: Bob Venero, President & CEO, Future Tech Enterprise, Inc., Ftei.com
Manufacturing is all about operational efficiency – make it quicker, cheaper, and ship it for less. For this reason, the industry has long been at the forefront of the application of new technologies, finding creative solutions to increase production and decrease costs.
Basically, how can we innovate faster while still prioritizing safety?
There is a mood of cautious optimism in the industry, and companies still wary of ongoing turbulence are using this time to invest in the future. In manufacturing – including manufacturing for Federal organizations and by Federal contractors – that future lies in artificial intelligence (AI).
Intelligent Design
A recent study from MeriTalk found that almost all – ninety-five percent – of Federal technology leaders feel that the appropriate use of artificial intelligence (AI) could supercharge the effectiveness of government and benefit the American people. Michael Shepherd, a senior distinguished engineer at Dell Technologies, says increased adoption of AI represents a “tremendous amount of opportunity” for Federal agencies, despite the workforce challenges.
Investing in AI “is going to make a difference,” Shepherd said in a recent interview with MeriTV. “I guarantee you, it’s happening in other countries, and we need to have that same level of investment here in the U.S. as well, especially within the armed forces and the Federal government.”
One of the many areas where that impact is significant is within manufacturing – from smart factories that can adjust production to meet evolving needs; to predictive maintenance that reduces equipment downtime and maximizes fleet readiness.
Manufacturing has been going digital for about a decade, leading some to christen this period the “Third Industrial Revolution”.
Direct automation, reduced downtime, 24/7 production, lower operational costs, greater efficiency, and faster decision making are just some of the rewards on offer to organizations that embrace the transformation and master the implementation of AI throughout their entire business.
The process of introducing AI is not without its challenges – it’s highly complex, costly, time-consuming, and requires a systematic approach. Just four in ten Federal IT leaders say they feel completely prepared for AI project implementation, with the lack of resources and available talent noted as the biggest roadblocks – ahead of budget.
But those that jump in earliest will gain a competitive edge. For example, John Deere debuted a fully autonomous tractor during CES 2022, powered by artificial intelligence and in development for over 20 years. The technology is now advancing so rapidly that organizations that don’t make their move into AI soon will find themselves falling behind.
Three Areas of Transformation
AI in manufacturing is often associated with futuristic robots, and for good reason. According to Global Market Insights, the industrial robotics market is forecasted to be worth more than $80 billion by 2024. But most (if not all) AI applications are software, and can improve a wide variety of functions for a manufacturer.
- Maintenance – In manufacturing, the greatest value from AI can be created by using it for predictive maintenance(generating more than $0.5 trillion across the world’s businesses). AI’s ability to process massive amounts of data means it can quickly identify anomalies to prevent breakdowns or malfunctions. The problem is getting that data. To scale requires more data, which requires more computing power to process. In fact, data preparation for AI systems is still 80-90% of the work needed to make AI successful.
One workaround might be the use of synthetic data, created “algorithmically” instead of real-world. Manufacturers are able to use synthetic data to build “digital twins” of their own datasets to test performance, improve functionality, and speed-up development so they can scale faster.
Enabling users to create precise digital twins is one thing Future Tech’s partner, NVIDIA, is making easier with its NVIDIA Omniverse Enterprise.
NVIDIA Omniverse Enterprise is a virtual environment enabling creators, designers, and engineers to connect major design tools, assets, and projects to collaborate and iterate in a shared virtual space.
Omniverse Enterprise is built on NVIDIA’s entire body of work, allowing users to simulate shared virtual 3D worlds. Here is the key part: these shared virtual worlds obey the laws of physics.
And, by doing that, Omniverse Enterprise enables photorealistic 3D simulation and collaboration. This in turn allows users to simulate things from the real world that cannot – and in many cases should not – be first tested in the real world.
To date, NVIDIA has demonstrated great success for Omniverse Enterprise in numerous industries, including aerospace, architecture, automotive, construction and design, manufacturing, media, and sensors.
- Safety – Optimizing safety on the factory floor is a critical consideration for any manufacturer. Advanced technologies are now focused on how to improve both factors at the same time.
Recent advances in AI can help catch compliance violations, enhance plant processes, and support better design and process flows.
Other AI-powered safety measures include being able to immediately detect whether employees are wearing the right type of gloves or safety goggles for a specific situation. Background process analytics can also be run to estimate potential for fatigue, reminding people when to take breaks.
- Quality Control – Within the manufacturing industry, quality control is the most important use case for AI. Everybody makes mistakes, even robots. Defective products and shipping errors don’t just cost companies millions, they also damage reputations and jeopardize safety. Now, AI can inspect the products for us.
Using special cameras and IIoT (industrial internet of things) sensors, products can be analyzed by AI software to detect defects automatically. The computer can then make decisions on what to do with the defective products, cutting down on waste. Better yet, the AI will learn from the experience so it doesn’t happen again.
Futureproof
As advances in AI take place over time, one day we might see fully-automated factories, product designs created with limited human oversight, and innovations we have not yet considered. Smart manufacturing environments will be there to help us build them.